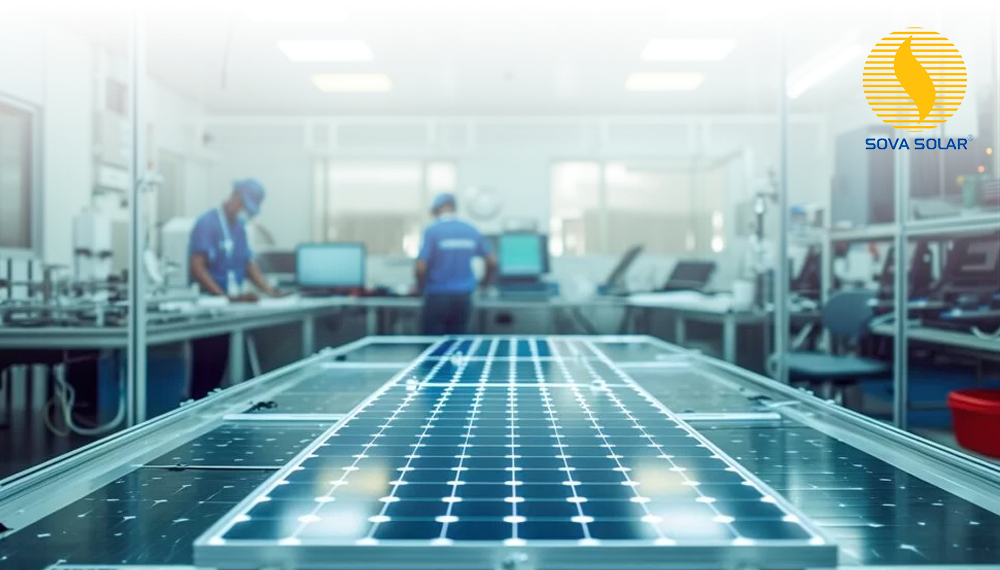
- sovasolar_admin
- Aug 27, 2024
- Uncategorized
- 0 Comments
In the solar industry, the quality of solar panels is paramount. At Sova Solar, we understand that the longevity and performance of our products directly impact our customers’ investment and the overall adoption of solar energy. This is why we place such a strong emphasis on quality control throughout our manufacturing process. Let’s delve into the critical role of quality control in solar panel production and how it ensures durability and reliability.
The Importance of Quality Control in Solar Manufacturing
1. Quality control in solar panel manufacturing is not just about meeting industry standards; it’s about exceeding them. Here’s why it’s so crucial:
2. Performance Assurance: Rigorous quality control ensures that each panel performs at or above its rated capacity.
3. Longevity: Well-made panels last longer, providing better return on investment for customers.
4. Safety: Strict quality measures prevent potential hazards like short circuits or fire risks.
5. Brand Reputation: Consistently high-quality products build trust and loyalty among customers.
6. Warranty Support: Robust quality control reduces warranty claims and associated costs.
Sova Solar’s Quality Control Process
At Sova Solar, our quality control process is comprehensive, covering every stage of production:
1. Raw Material Inspection
Before production begins, we meticulously inspect all incoming materials:
1. Silicon wafers are checked for purity, thickness uniformity, and structural integrity.
2. Glass is inspected for optical clarity and strength.
3. EVA (Ethylene Vinyl Acetate) sheets are tested for proper crosslinking and adhesion properties.
4. Backsheets are examined for durability and moisture resistance.
5. Cell Production Quality Control
During cell production, we employ several quality checks:
1. In-line electroluminescence (EL) testing to detect micro-cracks and other defects.
2. I-V curve testing to ensure each cell meets performance specifications.
3. Visual inspection for consistent color and absence of visible defects.
4. Module Assembly Quality Assurance
As cells are assembled into modules, we conduct:
1. Lamination quality tests to prevent delamination issues.
2. Junction box attachment and sealing inspections.
3. Final Product Testing
Before a panel leaves our facility, it undergoes a battery of tests:
1. Flash testing to verify power output and efficiency.
2. EL imaging to detect any cell damage that might have occurred during assembly.
3. Insulation resistance testing to ensure electrical safety.
4. Visual inspection for cosmetic defects and proper labeling.
5. Environmental Stress Testing
We regularly subject sample panels to stress tests that simulate years of real-world conditions:
1. Thermal cycling tests to check for resilience to temperature fluctuations.
2. Humidity-freeze tests to ensure moisture resistance.
3. Mechanical load tests to verify structural integrity.
4. Salt mist corrosion testing for panels destined for coastal areas.
Advanced Quality Control Technologies
To maintain our high standards, we invest in cutting-edge quality control technologies:
1. Automated Optical Inspection (AOI): AI-powered systems that can detect minute defects invisible to the human eye.
2. X-ray Inspection: For examining internal components without disassembly.
3. Thermography: To identify potential hot spots that could lead to performance issues.
4. Data Analytics: We use big data analytics to identify trends and potential issues in our production process, allowing for continuous improvement.
5. Ensuring Longevity Through Quality Control
The lifespan of a solar panel is directly tied to its manufacturing quality. Here’s how our quality control measures contribute to longevity:
1. Preventing Micro-cracks: Our careful handling and inspection processes minimize micro-cracks, which can expand over time and reduce panel efficiency.
2. Ensuring Proper Sealing: Rigorous testing of EVA encapsulation and backsheet adhesion prevents moisture ingress, a common cause of panel degradation.
3. Minimizing Potential Induced Degradation (PID): Through material selection and manufacturing processes, we minimize the risk of PID, which can significantly reduce panel output over time.
4. Robust Framing: Our frame attachment process and quality checks ensure that panels can withstand years of environmental stresses.
5. Performance Validation
Beyond our in-house testing, we regularly submit our panels for independent testing and certification:
1. IEC certification for safety and performance standards.
2. UL listing for North American markets.
3. Participation in voluntary reliability and durability testing programs.
4. The Human Element in Quality Control
While we leverage advanced technologies, the human element remains crucial in our quality control process:
1. Experienced Quality Control Specialists: Our team includes industry veterans who know what to look for beyond automated checks.
2. Continuous Training: We invest in ongoing training to keep our team updated on the latest quality control methodologies.
3. Culture of Quality: Every employee, from production line workers to management, is empowered to flag potential quality issues.
4. Continuous Improvement
Quality control at Sova Solar is not static. We continuously refine our processes:
1. Regular audits of our quality control procedures.
2. Feedback loops from customer service to manufacturing.
3. Collaboration with research institutions to stay abreast of the latest in materials science and manufacturing techniques.
Quality control is the unsung hero of solar panel manufacturing. At Sova Solar, it’s the backbone of our operation, ensuring that every panel we produce meets the highest standards of performance and durability. By investing in rigorous quality control processes and technologies, we’re not just manufacturing solar panels; we’re crafting reliable, long-lasting energy solutions that our customers can depend on for decades.
In an industry where performance and longevity translate directly into customer satisfaction and environmental impact, our commitment to quality isn’t just good business—it’s our contribution to a sustainable future.